Несколько решений от металлургов и для металлургов
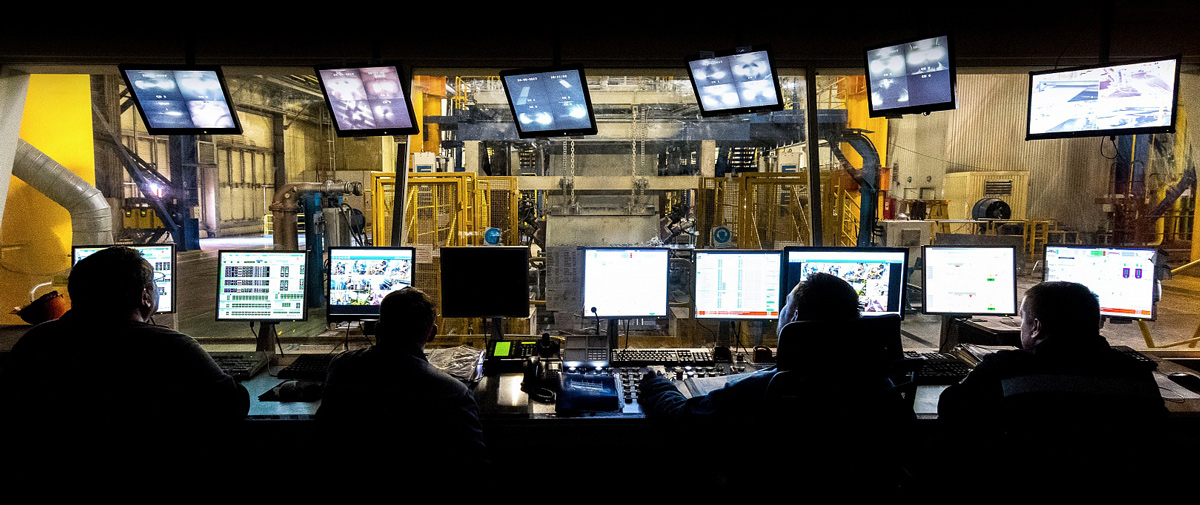
Дмитрий Шнайдер
научный руководитель группы математического моделирования и аналитики ММК, профессор ЮУрГУ
Сейчас на ММК реализуется стратегия цифровизации, включающая портфель проектов с общим бюджетом более миллиарда рублей. А для управления этим портфелем в компании создано новое подразделение — цифровой офис. Цифровые технологии ММК направлены одновременно на операционную эффективность производства, повышение качества продукции, безопасность и экологию.
А в текущих условиях мы можем, наверное, говорить о глобальной цифровизации. В связи с необходимостью организовать удаленную работу в процесс постепенно включаются работники практически всех поколений, уровней управления и профессий. Сейчас многие устоявшиеся консервативные привычки промышленников меняются независимо от возраста и должности. И мы ожидаем, что цифровые проекты будут получать все большее распространение во всех сферах производства.
Семь эпизодов ММК
- Модернизация корпоративной информационной системы до новейшей версии Oracle E-Business Suite R12 и расширение ERP-системы на общества группы — масштабная программа, связанная с оптимизацией и унификацией бизнес-процессов. Единая информационная система включает управление производством, запасами, ремонтами, закупками, финансами, персоналом, проектами, заказами и продажами.
- Внедрение решений в анализе массива данных помогает строить математические модели, чтобы перейти на интеллектуальное управление процессами производства. В первую очередь это касается оптимизации агло-коксо-доменного производства, на которое приходится более 70 процентов себестоимости выпускаемой металлопродукции. Здесь мы внедрили комплекс математических оптимизационных моделей для закупки угольного и железорудного сырья, а также для управления режимами работы доменных печей. Технологии модельно-упреждающего управления и машинного обучения успешно применяются и в других производственных процессах комбината. В частности, с их помощью решаются задачи, связанные с управлением производством, продажами и качеством продукции.
- Автоматизированная система оперативно-календарного планирования производства — сложнейшая разработка. Эта система просчитывает технологическую цепочку от приема заказа до выпуска продукции.
- Промышленный интернет вещей — одно из перспективных направлений в области анализа и управления производственными процессами, уже доказавшее свою эффективность. Наиболее успешно на ММК прошла испытания беспроводная система онлайн-мониторинга технологических параметров «ПолиТЭР-IIoT», разработанная совместно Южно-Уральским государственным университетом и компанией «Политех-Автоматика». Среди ее преимуществ — возможность мониторинга в самых сложных производственных условиях, длительное время автономной работы датчиков (не менее пяти лет), а также отсутствие необходимости создавать отдельные инженерные коммуникации для ее установки.
- Цифровой проект в экологии — создание автоматизированного комплекса, позволяющего оценивать ситуацию с выбросами в режиме реального времени и своевременно принимать меры для снижения воздействия на окружающую среду. Аналога настолько сложной системы в мире нет.
- Цифровые двойники оборудования: сейчас, когда становится востребованной возможность удаленного контроля за производственными процессами, мы вернулись к проекту по их созданию. Эти разработки позволят нам моделировать различные производственные сценарии, в том числе внештатные ситуации, и подбирать наиболее эффективные решения.
- Технологии виртуальной реальности — также сложная, но интересная задача. С помощью VR мы планируем развивать промышленный туризм, проводить удаленное обучение сотрудников, а в будущем, возможно, и перенести многие бизнес-процессы в виртуальную среду.
(Комментарий подготовлен с участием Данилы Целиканова, начальника цифрового офиса ММК.)
Кстати
Использование датчиков помогает металлургическим компаниям экономить ферросплавы и предотвращать окисление стали. Например, платформа Fero Labs позволяет повысить точность прогнозов возможных сбоев до 80-100 процентов и сократить их количество на 15 процентов. Информация с датчиков на фабрике поступает в облако, где они обрабатываются с помощью алгоритмов машинного обучения. Система делает выводы о возможностях для увеличения объема производства, предотвращения поломок оборудования и сокращения отходов.
У большинства производителей датчики уже установлены, но пока немногие компании могут должным образом воспользоваться полученными данными. Скажем, на одном из сталелитейных заводов установили 12 тысяч датчиков, но до недавнего времени активно использовали информацию только от пяти (!) из них. Fero Labs увеличила использование датчиков в 40 раз. Ранее невостребованные данные стали обрабатывать, а руководство компании исчерпывающую информацию о работе завода без установки какого-либо нового оборудования.
Историй успеха становится все больше, ускоряется темп изменений. Это говорит о том, что цифровая трансформация получила развитие в нашей компании.
Сергей Казанцев
директор по цифровой трансформации НЛМК
Например, мы перешли на 4D-проектирование объектов строительства, что позволяет еще на ранней стадии избегать возможных ошибок. Мы создали цифровой двойник карьера Стойленского ГОК и можем моделировать разработку месторождения минимум на 30 лет вперед. Цифровой сервис, оптимизирующий темп выдачи слябов в цехе горячего проката, позволяет повысить производительность одного из ключевых агрегатов группы — стана-2000. Модель оптимальной шихтовки сырья для доменных печей выравнивает химический состав агломерата и тем самым сокращает затраты кокса при выплавке чугуна. Мы внедрили решение с использованием нейронных сетей и машинного обучения в колпаковых печах. И оно помогает нам экономить электроэнергию при отжиге стали, рекомендуя оптимальное время для установки колпаков на нагревательных стендах.
Таких примеров много. Но важнее то, что количество «потенциальных» идей (то есть концепций цифровых продуктов, обладающих высоким потенциалом с точки зрения реализации и получения экономического эффекта) растет.
СОВЕТУЕМ ПОЧИТАТЬ
Наша компания вместе со Сколтехом создает инновационную технологию для повышения эффективности сталеплавильного производства на базе надежных пассивных беспроводных датчиков температуры охлаждающей среды и интеллектуальной системы обработки данных.
Владимир Калинин
первый заместитель генерального директора и директор по науке научно-технического центра «РУСЬ», выпускник акселератора GenerationS
В основе этой технологии лежит система, которая контролирует температуру среды охлаждающего контура в зоне вторичного охлаждения (он создается специальными форсунками), а также на ранней стадии предупреждает о необходимости заменить засоренные форсунки.
Система состоит из трех основных компонентов. Первый — сенсорная часть, надежные пассивные беспроводные температурные датчики комплекса RFSens BTC от НТЦ «РУСЬ» (они опрашиваются по радиоканалу специальным радиоэлектронным модулем-считывателем). Второй — цифровой двойник процесса непрерывного литья заготовок, разработанный Сколтехом. Третий — рекомендательная часть, позволяющая прогнозировать время засорения форсунок, отслеживать в режиме онлайн их температурные состояния и определять сам факт засорения.
Интеллектуальная система строится на основе численной модели засорения. Данные от датчиков, установленных на форсунках, позволяют строить температурные тренды и формировать прогноз засорения. А использование цифрового двойника дает возможность определить время выхода деталей из строя и рассчитать степень повреждения сляба с учетом прогнозируемого охлаждения. Если значения достигают критического уровня, система выдает рекомендацию заменить форсунки. Затем строится карта с точными координатами засоренных форсунок, которую сотрудники производства используют при выполнении планово-предупредительных работ.
Предиктивная аналитика охлаждающего оборудования и контроль его параметров в онлайн-режиме помогут качественно повысить эффективность сталеплавильного производства.
В настоящее время температурные комплексы RFSens BTC апробируются в режиме опытно-промышленной эксплуатации в нескольких компаниях: «Вымпелкоме», МОЭСК, «Сибуре» и других, — а созданную на их основе технологию для сталеплавильного производства планируется внедрить в «Северстали».
Справка
Научно-технический центр «Радиотехнические устройства и системы» («РУСЬ») — инновационная компания, резидент «Сколково» с 2015 года. Торговая марка компании — RFSens. В росте компании участвуют ведущие отраслевые инвестиционные фонды и институты развития: TerraVC, РВК, фонд «Сколково». Эксперты федеральных конкурсов GenerationS и «Энергопрорыв» признали проекты компании лучшими технологическими решениями в области энергетики.